Choosing the perfect pushrod wall-thickness and outer diameter is a careful balance between weight and strength.
A few years back, an observant engine guy was visiting Kenny Duttweiler’s shop on a pleasant Southern California summer afternoon. In one corner of the shop floor sitting on an engine stand was a Pro Mod–style big-block with its intake manifold removed. Ken was on the phone and the visitor was admiring the engine when he noticed the size of the pushrods. They looked like ½-inch drive socket extensions compared to the wimpy set of 5/16-inch rods he had in his hand. He went over to the tool box and grabbed a 9/16-inch open-end wrench and tried to slide it over the outside of the pushrod body. It didn’t fit. He had to use a 5/8-inch wrench to make it fit. Welcome to the world of high output drag race pushrod engines.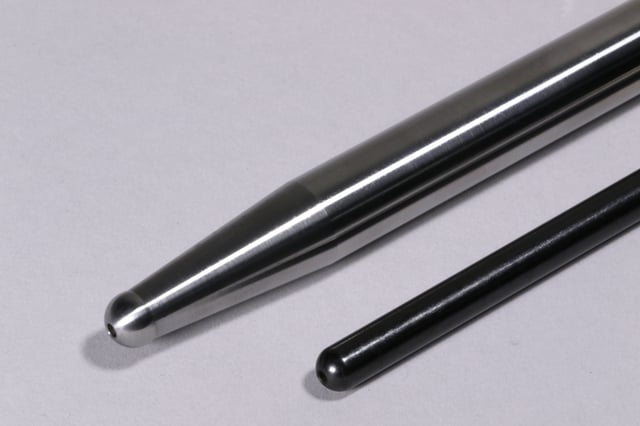
Kinematics is a fancy term for the violence that occurs inside a race engine at high speed with 1-inch-plus valve lifts and ionospheric (that would be north of the stratosphere) rpm levels. Trend’s Design Specialist, Andy Anderson makes the approach simple. “The more material in a pushrod the stronger it is. You use taper to get the clearance you need and add material.” Let’s dissect that statement to pull even more meaning out of it.
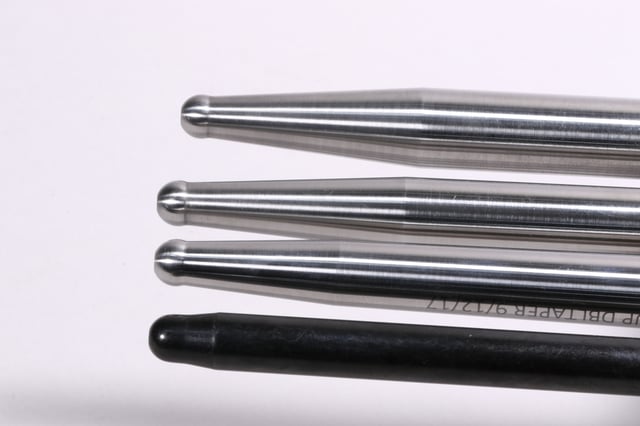
Since pushrod length is mostly a matter of connecting the lifter to the rocker, the length will be a set dimension. But that leaves plenty of other options in terms of diameter and wall thickness. Even within the smallest 5/16-inch diameters, there are options that can add strength. Trend’s standard pushrod offers an 0.080-inch wall piece but that strength can be immediately enhanced with the addition of 0.105-inch wall thickness option. This is more than a 30 percent increase in wall thickness that automatically guarantees a much stiffer pushrod.
Often a greater wall thickness is the only option when tight real estate concerns prevent upgrading the pushrod diameter. While often true with small-blocks, big-block engines often can benefit from additional room that offers multiple opportunities. For a typical big-block Chevy for example, increasing the pushrod diameter from 3/8- to 7/16-inch may not present a clearance problem and offers a simple solution to improve performance.
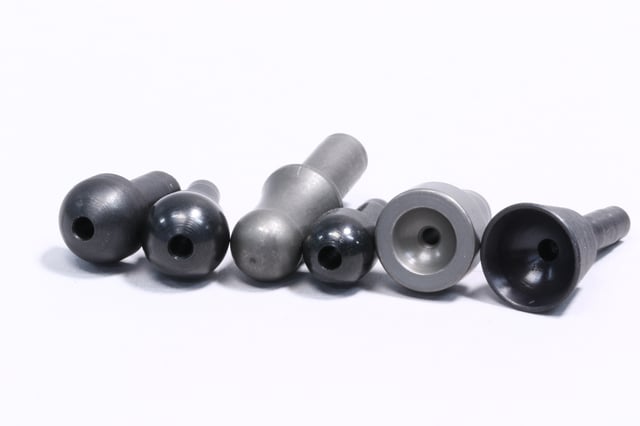
But larger intake ports quickly begin to impose space limitations that require pushrod designers to become more creative. Single and double tapered pushrods offer a way to increase overall compressive strength while offering the clearance needed either at or near the rocker arm or down at the lifter – oftentimes in both places.
There are actually four different Trend taper styles for the larger diameter pushrods. These include a full, half, double or neck-down taper designs. Some are dictated by clearance concerns but tapering can also be used to enhance strength. According to Anderson “ Our double taper 7/16-inch provides the customer a stiffer pushrod that will still work in most 3/8-inch pushrod assemblies.”
Wall thickness is another way to improve strength without adding diameter. Trend offers two options on wall thickness on most of its pushrod diameters which creates the opportunity to weigh the relative advantages of strength versus weight. In the past, concerns about weight seemed to override strength, but evidence generated by Bob Fox’s SPINTRON proves that in most cases strength trumps weight with regard to pushrods.
Trend Quick Ship Pushrod Program
Pushrod Diameter x Wall Thickness (inches) |
End Style (degrees) |
Double Taper Optional |
Length (inches) |
Quick Ship Program |
5/16 x 0.080 |
180 Ball |
No |
5.85 - 11.050 |
No |
5/16 x 0.105 |
210 Ball |
No |
7.00 - 9.650 |
No |
3/8 x 0.080 |
210 Ball |
Optional |
6.00 – 12.250 |
No |
3/8 x 0.135 |
210 Ball |
Optional |
7.00 – 10.175 |
Yes |
7/16 x 0.165 |
210 Ball |
See Below |
7.00 – 11.950 |
Yes |
7/16 x 0.165 double taper |
210 Ball |
Standard |
7.00 – 11.500 |
Yes |
½ x 0.200 |
210 Ball |
Standard |
8.00 – 11.000 |
Yes |
9/16 x 0.187 |
210 Ball |
Yes |
6.00 - 13.00 |
Yes |
5/8 x 0.125 |
210 Ball |
Yes |
6.00 – 13.00 |
Yes |
5/8 x 0.188 |
210 Ball |
Yes |
6.00 – 13.00 |
Yes |
One item to keep in mind here is that while weight is always a concern, it is less of an issue on the lifter side of the rocker arm since this side of the system’s total mass is only subjected to the acceleration dictated by the camshaft lobe. The issue of mass times acceleration that generates force becomes far more critical when multiplied by rocker ratios of 1.7:1 or higher.
We keep talking about loads, so let’s look at exactly what the pushrod is experiencing. A typical Pro Mod motor might need around 300 pounds of closed valve spring pressure and 1,400 pounds of open valve load. While that number alone is impressive, it’s somewhat conservative when you consider that if the rocker ratio is 1.7:1, then the pushrod must be able to easily withstand a load of 2,380 pounds (1,400 x 1.7) – or roughly equivalent to supporting the weight of the entire race car on that small column.
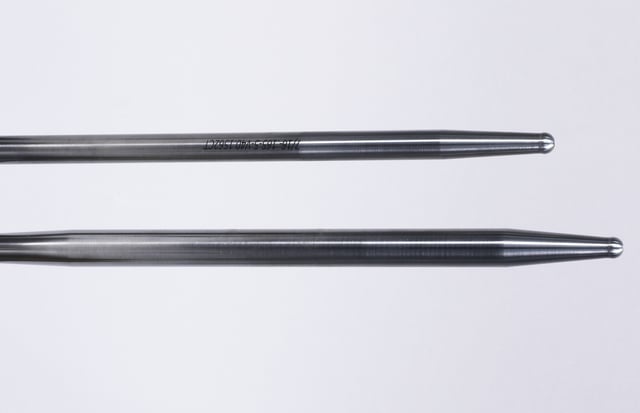
But these are just static loads and do not take into account the physics of the force = mass times acceleration formula. If we take what is commonly assumed to be conservative valvetrain acceleration rates of 100 g's at an equally conservative 6,000 rpm, this jacks the load to nearly 240,000 pounds. These are instantaneous loads but what’s really scary is when deflection does occur loads can spike to well over 1,000 g’s. That’s when the numbers become very immense.
This is the reason for such large pushrod diameters and wide wall thicknesses when dealing with large displacement engines with ridiculous spring loads at equally outrageous engine speeds. The fact that these components survive this abuse is testament to the strength and durability of the Trend components.
QSP Pushrods
Diameter |
Wall Thickness |
5/16 |
0.105 |
3/8 |
0.135 |
7/16 |
0.165 |
1/2 |
0.200 |
9/16 |
0.187 |
5/8 |
0.125 |
5/8 |
0.188 |
H-13 |
Solid |
One place where that load is concentrated is right at the pushrod tip. Extreme cam lobe lift numbers push the rocker arm through a rather wide arc of travel. This requires that the pushrod body not interfere with the rocker arm throughout this travel. This requires some special attention in terms of a 180- or 210-degree radius around the end. This additional room just makes it easier for the components to work together.
Because pushrods are one of the last items ordered for a custom race engine, the engine builder often needs these parts delivered quickly. In today’s era of the I-need-it-now crowd, there usually is no time for the engine builder to wait for custom-made pushrods. Trend has responded with its Quick Ship Program (QSP) that offers thousands of pushrods in dozens of lengths and diameters with specific sizes in 0.025-inch lengths. This is just another example of how Trend understands the need and delivers.