The pushrod is one of the most used and abused components in an engine so choosing the right base material is paramount to a healthy street or race engine.
It would seem such a simple device – a pushrod. It has no moving parts yet the technology that goes into a Trend pushrod is worthy of closer inspection. For a production V8 pushrod engine, these pieces should preferably be a short, steel column with a couple of balls affixed to each end and a hollow center to allow oil to find its way to the rockers and valve springs. And for your trips to the grocery store, they work very well with a reasonable expectation of enduring hundreds of thousands of miles.
But drag racers care little for endurance situations. Making horsepower means stratospheric engine speeds, aggressive camshaft lobes, and rockers approaching 2:1 ratios, which not only double the lift, but also the load. Within the realm of the unpretentious pushrod, it would seem a simple task to transfer vertical travel from the lifter to the rocker arm. But with inertial loads that increase with the square of the engine speed (which means four times the load when we double the speed), it doesn’t take a theoretical physicist to figure out that adding rpm is going to be stressful on the pushrod.
Trend’s Bob Fox quickly learned after developing the SPINTRON that the pencil-like pushrod is downright abused. Race engine builders used to abhor adding weight to any component because that meant adding mass to the valvetrain which meant increased force the spring has to control. While that is mostly true, the Spintron proved that a small-diameter, thin-wall pushrod was guaranteed to bend just like a pole vaulter’s lever. All that bending did much more harm than just rub on the cylinder block. It also stored energy that was later released at the wrong time, often crashing the lifter into the cam flank at an inopportune place.
Pushrod Materials
Material |
Tensile |
Yield |
Rockwell |
1020 |
57,250 |
42,750 |
Rc 71 |
4130 |
97,000 |
63,000 |
Rc 60 |
H 13 |
289,000 |
239,000 |
Rc 54-56 |
It quickly became apparent that making the pushrod stiffer could be rewarded with improved valvetrain stability. Since nearly all the load on a pushrod is in compression, this is essentially the same evaluation as a steel alloy’s compressive strength, which can be defined as the point at which the steel permanently deforms. Other important variables are of course the material’s ductility and shape.
There are several ways to go about making a pushrod stiffer. We’ll get right into the materials portion and leave the length and diameter questions for a later story. This aims us directly at an investigation of steel alloys. One of the simplest and best approaches to improving stability is to make the pushrod out of a stronger steel. As you can see from the Pushrod Materials chart, there is a dramatic improvement of tensile (compressive) strength just by moving from the production engine’s 1020 steel alloy to the more robust 4130 material. These tensile strength numbers will change based on how chrome molybdenum steel is heat treated, so the numbers in our chart are somewhat generic but representative.
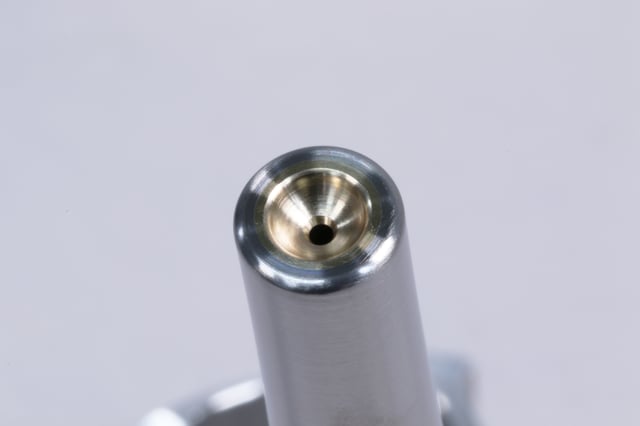
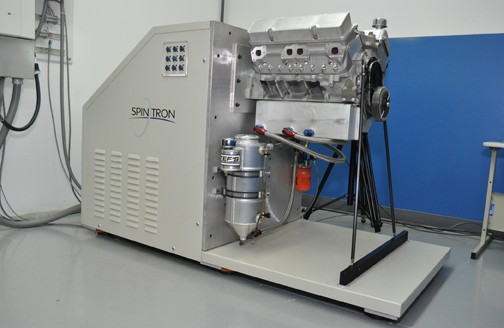
For these engines, cylinder pressures, especially for the exhaust pushrod, can be enormous. For this reason, Trend offers the H-series pushrods that are constructed from solid ½-inch billet tool steel blanks and custom-machined to the required specs. This material, while slightly softer in terms of Rockwell hardness, its tensile strength is nearly three times stronger than 4130. The beauty of this material is that it is not three times as brittle, in fact it is very similar in terms of elasticity compared to 4130, which is exactly what makes H-13 such a great material for a pushrod.
The top tier in Trend’s pushrod progression is the V40 program that uses a 5/16-inch self-lubricating tip that is hardened to 60c Rockwell. Both ends of the pushrod are formed offering 210 degree radius at the end of a 1 5/8-inch long taper for optimal clearance. These pushrods are available in 7/16-, ½-, and 9/16-inch diameters. Similar to the hard-tip pushrods, Trend offers the V-40 style using similar self-lubricating, Rc60 cup on the rocker arm end to accommodate the rocker arm adjusting ball. The V-40 pushrods are offered in lengths from 6.00 to 13 inches.
For a device so simple, we’ve seen that there is a constant dance between the engine builder and racer’s demand for more power and rpm and that of technology and metallurgy to push that along.