DLC coatings are some of the toughest coatings in the world and allow parts to operate in inhospitable conditions once thought impossible. Here is a deep dive into what they are and how they're applied in the racing world.
Automotive racing technology and its applications trickle down from the highest echelons of racing activity; in most cases, this is Formula 1, where teams spend astronomical sums of money looking for the most minute edge over the competition. As many of the performance advantages are tightly regulated by the ruleset, any area where an advantage can be gained is exploited to the extremes, and that's where low-friction hard coatings first entered the automotive performance realm. Prior to their arrival in the automotive performance arena, these coatings were used in applications such as helicopter gearboxes, where friction reduction is critical for performance reasons.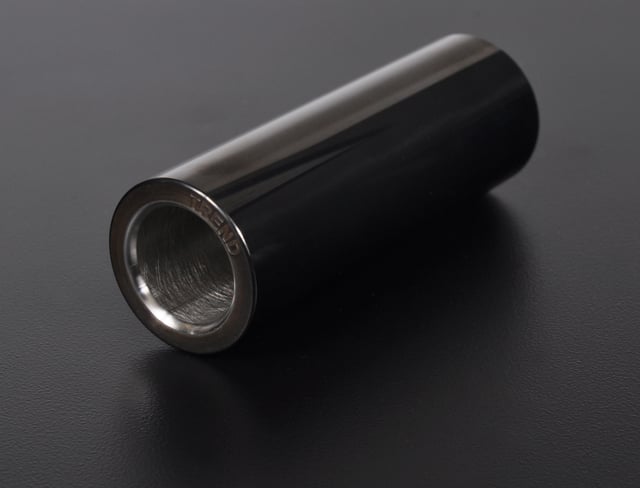
The most prominent of these coatings—Diamond Like Carbon, or DLC for short—has been propelled to the top of the food chain because of its amazing properties when applied to internal engine components. Comprised of layers of nano-crystalline diamond and nano-crystalline silicon carbide in an amorphous matrix of the two elements, DLC has extreme hardness, minimal thickness, and a favorable wear rate, making it ideal for use when applied to engine components. Basically, DLC combines the properties of diamond and graphite—since carbon creates both —to create a hard, yet slick, coating for internal engine parts.
There are several advantages to using parts coated with DLC film. Its properties include increasing the lifespan of parts by reducing the coefficient of friction. This also lowers the chance for surface fatigue and potential failures. The film protects the surface of parts treated with the process, which can prevent abrasions of the material and help to maintain unrestrained movement—good for pieces like piston pins, which need to move without hindrance.
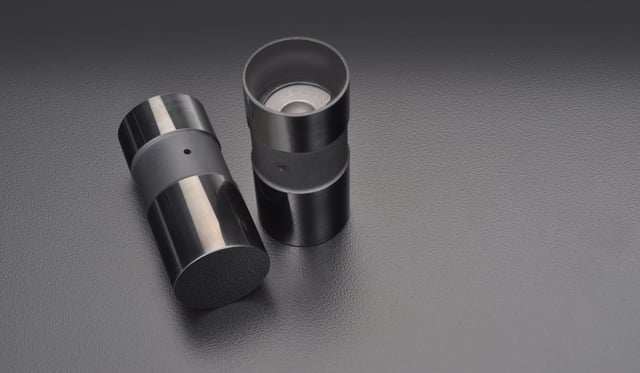
Its finish is incredibly smooth, with high lubricity. When DLC-coated parts are compared to bare metal parts, 50-percent or greater friction reduction with no lubrication is typical. Lastly, due to its characteristic as a stable layer applied to the underlying material, the DLC thin film coating can dramatically improve parts reliability since it does not react to acids or alkaline, and is resistant to corrosion and oxidation.
“With any type of power-adder engine, DLC adds lubricity and hardness, which prevents the pin from galling,” says Trend Performance's Bill Vinton. “It's also extremely helpful in applications where alcohol is used as the fuel, since the alcohol washes the engine oil away from the pin.”
Vinton views DLC as an insurance policy for the customer, as the thin film coating does not present any maintenance concerns or other challenges to its consistent use.
Trend Performance offers a premium DLC coating process for certain parts in its catalog, specifically its wrist pins, flat-tappet lifters used with billet camshafts, and valve locks. But it's not just any old DLC process. As Trend is a manufacturer of premium engine components used in those upper-echelon racing classes mentioned above, the choice of partner for DLC application was a critical step in the company being able to deliver the products its customers deserve.
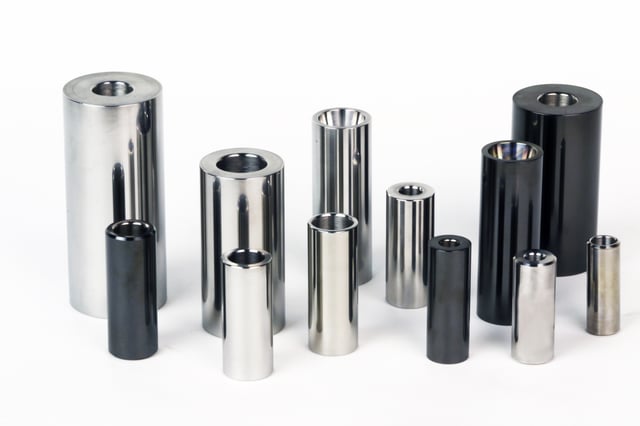
Enter Industrial Hard Carbon of Denver, NC, and its operations department, which is able to exceed the expectations of the Trend team from start to finish and provide industry-leading performance on every DLC-coated part in the Trend Performance catalog.
“In addition to having the industry’s leading hard carbon thin film, IHC maintains a commitment to quality that is second-to-none in the thin film industry. In many instances a coating may be good enough to meet the requirements of a specific application, but IHC has built its business by enabling customers to reach the highest potential that vapor deposition films can offer,” says Brent Johnson, IHC's Operations Manager.
How It's Applied
For thin film coatings like DLC, the application process is the heart of the product's performance, and having not only the proper machinery for application but the correct QC and testing methods to ensure its critical tolerances are held in check is paramount to the success of the coating in use.
Key among the properties of DLC is its ability to reduce friction on the components which need it most, like piston pins and valvetrain pieces, but the proper surface finish on the part prior to the application of the film is perhaps the most important step of the entire process.
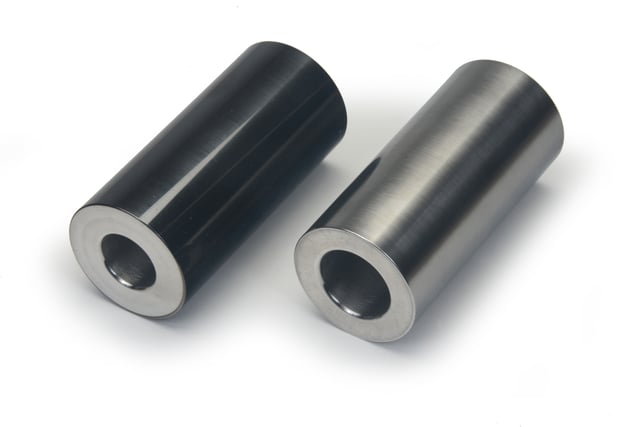
The finished part, prior to DLC application, must be finished to near-perfect dimensions to ensure the coating film adheres to the part properly and performs up to expectations.
“Most vapor deposition techniques rely on proprietary adhesion layers which form chemical bonds to the substrate material (the part) that they are trying to coat,” says Johnson.
How the company actually performs the vapor deposition process is withheld for competitive reasons, and we can't blame him. There's a reason IHC is at the top of the heap when it comes to DLC application.
“Because there are many different techniques to achieve adhesion, adhesive layers and/or their deposition processes are of significant economic and strategic value,” he says.
When we say that DLC is a film, you can't think of it in terms of something like window tint, which can be 100 micrometers thick. DLC is so thin that it falls within the tolerance for the finished part without the coating applied. It's amazing to think that a coating with such a small footprint can have such large benefits to the finished product, but it does.
“It is helpful to bear in mind vapor deposition coatings are generally only 1-6 micrometers thick (0.00004 – 0.00025-inch), which is within the tolerance of most finished parts. It is hence fairly easy to maintain the tolerance of the final part through the coating process,” says Johnson.
Quality Is Job One
The precision application process sets the stage for the quality of the final product, but that quality is also achieved through several methods during the manufacturing steps.
“IHC maintains a commitment to quality that is second-to-none in the thin film industry. In many instances a coating may be good enough to meet the requirements of a specific application, but IHC has built its business by enabling customers to reach the highest potential that vapor deposition films can offer. We do this by emphasizing attention to detail in inspection and coating, identifying the root cause of problems, and consulting with customers to ensure the part, coating, and application are well suited to each other,” says Johnson.